Energy efficiency, environmental pollution, and greenhouse gas/climate change issues have been in the forefront of international dialog and debate for decades now. For the United States, the incentive of energy independence brings added practicality to these issues. Energy efficiency is a key factor in these discussions. Much has been done over the past few decades. This ranges from advances in lighting and heating technologies to improvements in energy generation and overall energy efficiency.
These areas continue to develop, and new ideas are constantly emerging. However, this is not new to process industries such as petrochemicals, chemicals, food, refineries, and other general process industries. The economic balance of operational costs and capital deployment has driven efficiencies in these sectors for well over 50 years. As the cost of energy increases and societal concerns for climate change intensify, far more pressure is exerted on large process industry production facilities. They are expected to do even better and longer paybacks on capital are being accepted.
Energy Intensive Applications at Production Plants
The industrial sector alone uses approximately 54% of the world’s delivered energy. Oftentimes, industrial equipment intended to make an operation more sustainable only does so at the cost of increased energy usage. To ensure optimal results in energy savings, it’s important to identify key production areas where energy needs may be high. Therefore, implementing solutions that minimize this impact is crucial. RCM Thermal Kinetics focuses on this issue for every project.
Design Methods for Energy Usage Reduction
At RCM Thermal Kinetics, we employ the following design methods to mitigate energy usage on unit operations such as:
- Mechanical Vapor Recompression (MVR) MVR transfers heat from a stream of used vapor by elevating its pressure levels with a compressor and reusing it to capture its heat energy. As a result, this offers significant energy savings.
- Thermal Vapor Recompression (TVR) TVR uses a jet of steam to elevate the pressure and temperature of a waste vapor stream before transferring and reusing its useful heat energy.
- Multiple Effect Evaporators Evaporators with multiple effects require significantly less heating media, thus improving the energy efficiency of the evaporation process. The next effect uses evaporated water from the previous evaporation process as the heating media. This can occur over several effects, ensuring optimal energy efficiency.
- Multiple Effect Distillation Each distillation stage features a drop in pressure and temperature, allowing for reuse of the previous effect’s energy. Since this process only requires input energy for the first stage, it has very low energy consumption.
- In-System Energy Recovery Engineers can create many systems in such a way that the waste they produce can be recycled or treated into a suitable solution. Consequently, this will power future process cycles.
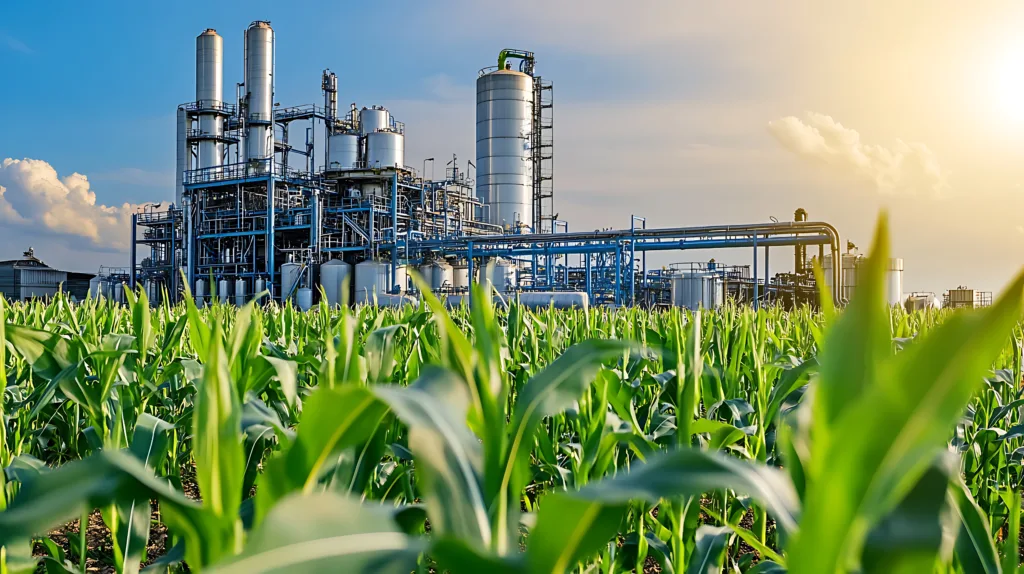
Common Applications for Energy Efficiency
Solvent Recovery Distillation
Common in industrial fields such as oil and gas or chemical production, solvent recovery has become a popular method for reducing waste in many industrial applications. By distilling solvent waste, manufacturers can separate solvents from other waste and recover them for reuse. This ultimately lowers the overall cost of manufacturing.
Waste Evaporation
Evaporation has been proven as an effective method to reduce the total volume of waste that goes into municipal sewage systems or landfills. Essentially, liquid waste is heated to boiling and the vapor is vented into the atmosphere or recycled back into a usable form. Many industrial operations have also found that they can recover useful byproducts from waste via the evaporation process.
Steam Strippers
Steam stripping is a common industrial process that separates wastewater from volatile organic compounds. The high temperatures required by this process tend to strip a larger volume of soluble organic matter from the wastewater. As a result, this has made this method more popular than other methods such as air stripping. The steam stripper produces a distillate that often contains a variety of VOCs mixed together, and operators typically send it offsite for safe disposal.
Evaporative Crystallization
Solids can be removed from waste and crystallized, significantly reducing the volume of liquid waste runoff. Often this liquid waste can be purified and then reused in some capacity. Alternatively, producers can safely release it into the environment or municipal sewer.
Stillage Evaporation
In ethanol production, producers must evaporate the stillage at the bottom of a beer column to produce usable animal feed. However, the stillage evaporation process is quite energy intensive and negatively impacts the sustainability of ethanol production.
Financial Incentives for Environmentally Friendly Process Equipment Systems
There are a variety of solid business reasons to implement sustainable process equipment in your facility. Some of these include:
- Lower energy costs. By streamlining the efficiency of your process equipment, organizations will save on fuel usage and lower energy bills. Given that process equipment typically uses large amounts of energy, any efforts to save in this area should provide significant ROI.
- Regulatory compliance. As renewable energy methods such as wind and solar become more popular, the regulations surrounding them will likely change and evolve. Companies who are on the forefront of sustainable technologies now will find themselves well-poised to meet increasing regulatory demands down the road.
- Tax credits. Many state and federal initiatives exist to reward companies for implementing sustainable practices. Installing process equipment that meets the requirements for these credits can offer significant savings come tax time.
- Less waste. By design, environmentally friendly process equipment systems will use and/or process materials more efficiently, which will positively impact material costs. This also results in less material waste, reducing overall disposal costs.
To learn how RCM Thermal Kinetics can help your facility implement sustainable process equipment, contact us today.